
In 2000, Leonard's Carpet Service, Inc. of Southern California developed a stone division to produce countertops as requested by many of its customers. Today, the 31,000-square-foot facility, located in Perris, CA, produces an average of 5,550 square feet of stone per week.

The company's shop is equipped with an OT 1500 Intermac Master Stone CNC stoneworking center from AGM.
“We began as a carpet installation company in the 60s, and through the 70s and 80s we began to add other products such as sheet vinyl, hardwood flooring and ceramic tile,†explained Jonathan Segaar, the company's countertop division manager. “We have always focused on residential new construction installations and during the late 90s many of our customers began to ask us to do countertop installations.†In 2000, to meet customer demand, the company hired subcontractors to template, fabricate and install granite countertops. “We soon realized the demand for granite countertops was growing. In 2002, we began doing some of our own granite countertop installations, and in 2003, we opened a fabrication facility here in Perris [CA].â€

The OT 1500 is equipped with a versatile and powerful CAD-CAM system and offers a large worktable measuring 1500 x 3000 mm.
According to Segaar, two significant pieces of machinery enabled the company to increase its production rate. “When we added our Comandulli Omega 100 edge machine, distributed by AGM, we saw our production jump,†he said. “The quality of the edge detail this machine produces is excellent, and the capacity of the machine exceeded my expectations. We run our Omega 100 for about 20 hours each day. This machine performs very well. We've had very little down time on this machine due to repairs.â€
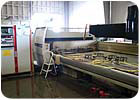
The company also utilizes a Pro Series CNC stoneworking center, which is a new Intermac machine from AGM.
Leonard's Carpet Service recently switched its stone shop over to digital templating, and it operates four LT-55 precision laser templators from Laser Products Industries of Romeoville, IL. “Digital templating seems to complement the CNC saws and CNC routers very well,†the fabricator explained. “Our template makers are able to get templates in about half the time, and the images they capture are generally more accurate than the stick templates. The fabrication shop is able to process jobs much faster when using digital templates. The CAD files are already created in the field, so it saves our CNC programmers a lot of time.

The shop is also equipped with an AIM Mastercut 2400 CNC machine from AGM, and a second one is on its way. “This saw can easily do the work of two or more manual saws,†said Jonathan Segaar, the company's countertop division manager. “When we added this saw to our shop, our production jumped.â€

The company uses a Marmo Meccanica LCV 711 M backsplash processing machine from Marmo Machinery USA to flat polish backsplashes.
Employee operations
Today, the stone division consists of two nine-hour shifts with 20 employees on each shift. According to Segaar, employees are generally trained to do one specific job, starting in either the lamination area or the polish area, and then they work their way into other positions. Most of the company's employees are hired by word of mouth, and on-the-job training has provided successful results.“In the last two years, we've probably trained close to 20 CNC programmers and operators,†Segaar said, adding that the biggest obstacle he has faced during training are the trainees themselves. “The CNC machines seem complicated when you first look at them. Most people become very intimidated when they first begin training. By week three, the trainees are able to perform most functions on their own. When learning to program and operate for CNC machines, mind set is very important. It is impossible to learn all CNC skills in one day, but if you break down the training into manageable pieces and learn a few pieces each day, in a few weeks, you'll be a pro.â€

Workers in the shop use hand polishers for finishing, and two Torit dust collection units are also in place at the facility.

The company relies on an overhead crane system from Demag Cranes and Components of Cleveland, OH.

Perris, CA
Type of work: residential work, including flooring, countertops and vanity tops
Machinery: a Camma bridge saw from AGM of Pineville, NC; a manual bridge saw from TE.CO. Macchine of Italy; a Flow waterjet from Flow International Corp. of Kent, WA; two Intermac CNC machines - an OT 1500 and a ProModel - from AGM; a Marmo Meccanica LCV 711 M backsplash processing machine from Marmo Machinery USA; a Comandulli Omega 100 edging machine from AGM and an AIM Mastercut 2400 CNC machine from AGM (with a second one on its way); two Torit dust collection units; four LT-55 precision laser templators from Laser Products Industries; an overhead crane from Demag Cranes and Components of Cleveland, OH
Number of Employees: 20 employees per two nine-hour shifts
Production Rate: 5,550 square feet a week