Stone World recently had the opportunity to ask several leading industry professionals about the latest trends in quartz and porcelain slab lines, as well as the education being provided to fabricators about cutting and installing these materials. Those we spoke with included:
- Marty Davis, Chief Executive Officer (CEO), Cambria
- Arik Tendler, Chief Sales Officer (CSO), Cambria
- Lori Shapiro, public relations and corporate communications manager for North America, Caesarstone
Here is what they had to say:
SW: Why do you think materials such as quartz surfacing and porcelain slabs have become so popular?
AT: Quartz surface products are popular for a number of reasons. Design and durability are critical reasons for quartz's success in the countertop and surfaces industry. Furthermore, quartz surfaces boast inherent qualities that make it an attractive option for homeowners and designers alike. It is non-absorbent and hygienic, making it a great choice for kitchens and bathrooms. It is also easy to maintain and does not require sealing, polishing or reconditioning.
At Cambria®, we have an inventory of the most stunning designs in the industry and, the durability and low-maintenance properties create added value. In particular, the quartz used in our products is the highest quality in the world, resulting in a visually striking product that is difficult to match in the industry.
LS: Quartz and porcelain have always been excellent choices for countertops, but in more recent years, we have seen these two materials become the top favorites. Both materials offer extreme durability with stunning designs. The key differentiator between the two is that porcelain can withstand much higher heat and mimics the beauty of natural stone, but with added durability with our unique mesh backing. With outdoor living being a growing trend, we offer the only outdoor quartz on the market, and porcelain surface options that are weatherproof, durable and will not fade with UV rays. Caesarstone Porcelain is specifically designed for countertops for a new point of view on how to use this material in the industry.
SW: You have been a quartz producer for many years. How has the manufacturing process evolved?
MD: Quartz manufacturing evolution varies by producer and has a wide-range of developments. The costs of manufacturing have increased greatly, while the techniques employed have allowed for more movement and interaction amongst an aesthetic within a surface.
As a quartz producer with nearly 25 years of experience, we have always placed a strong emphasis on innovation to create the best quartz surfaces possible. As technology advances, we have been able to further refine our manufacturing process and develop new techniques to improve the quality of our products and create game-changing designs like our latest Alloys collection.
In particular, we have invested heavily in research and development to find new ways to enhance the durability, performance and aesthetics of our quartz surfaces. This has resulted in the development of never done before manufacturing processes that allow us to create quartz products that are unique. We have an excellent R & D team. They are in the business working relentlessly to evolve our processes and techniques. They are constantly challenging each other and testing technological limits to improve our production capabilities and create innovative new products that meet the needs of our customers.
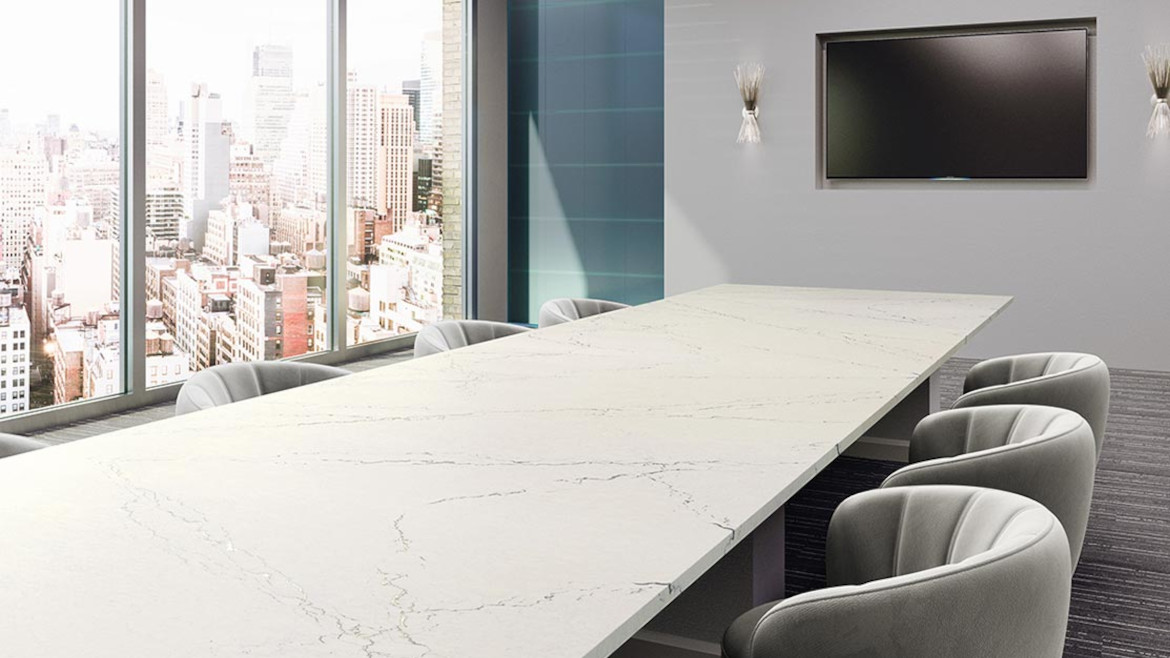
"Design and durability are critical reasons for quartz's success in the countertop and surfaces industry," said Arik Tendler, Cambria Chief Sales Officer (CSO). | Photo courtesy of Cambria
Overall, our commitment to staying at the forefront of pioneering advancements in the quartz industry has enabled us to deliver some of the best quartz surfaces in the world, and we will continue to leverage new technologies and refine our processes to meet the evolving needs of our customers. We compete with very good companies in our industry, all who do excellent innovative work for the industry as well!
LS: At Caesarstone, innovation is at the core of who we are. After pioneering quartz over 30 years ago, we took the next step to expand our portfolio to offer porcelain and natural stone to give our customers all the materials they need in one place. The global R&D teams constantly innovate by bringing industry firsts to the market. Our Outdoor Quartz collection is the only one on the market, bringing the beauty and durability of quartz to outdoor living, withstanding UV rays and extreme temperatures. Our ultra-rough concrete finish brings a tactile industrial look that has been very popular recently. And, the fiberglass mesh backing in our new porcelain line is revolutionary -- essential for our fabricators. Our porcelain line in ultra-rough and honed finishes offers a new point of view on what countertops can feel like in the home. As part of our sustainability mission, we have established a domestic footprint by opening our U.S. manufacturing plant in Savannah, GA. We are also proud to be the only surface provider with a third-party verified Declare Label, delivering complete transparency about product ingredients to help architects and designers meet strict LEED certifications and sustainability standards for their projects.
SW: When developing new product lines, what are some considerations you take into account?
MD: When developing new product designs, Cambria takes several important considerations into account. First and foremost, we make a concerted effort to listen to our partners and customers, including fabricators, installers, designers, architect's, builders, kitchen and bath dealers and consumers. We value their feedback and insights, as they often have a unique perspective on what they need and want in a new product. We also try to keep a very open-mind as to what a surface can become both aesthetically and in performance.
Key consideration when developing new product lines is always ensuring that our products are not only visually appealing, but also highly functional and durable. We carefully evaluate the performance characteristics of each new product, such as its resistance to staining and scratching, to ensure that it meets the needs of our customers and can withstand the demands of everyday use.
Finally, we strive to stay on the cutting edge of design trends and industry developments, while also ensuring that our products are timeless and will maintain their appeal for years to come. By taking these considerations into account, we are able to develop new product lines that not only meet the needs of our customers, but also exceed their expectations and further expand markets, even beyond expectations of the market.
LS: There are two ways Caesarstone goes about developing new product lines. The first is identifying gaps in the industry to trail blaze innovation by bringing cutting-edge designs and unparalleled durability to the market. At Caesarstone, we are proud to be a one-stop-shop. You can trust we have all the materials you need in one convenient place. The second consideration is what inspires our design team and brings warmth to the heart of the home. Many of our designs are based on what one may see or find in nature, which is our biggest inspiration. We believe that materials from the Earth should bring tranquility and warmth into any space, and we want to give our customers that experience in their home.
SW: What measures do you take to educate fabricators about cutting quartz and porcelain slabs?
AT: At Cambria, ensuring that both Cambria and our fabricators partners are well-informed about processing, fabricating and finishing quartz is essential to the quality of our products, and to the safety of each party involved and ultimately the satisfaction in all of our collective customer's experience. To this end, we have taken several measures to provide comprehensive learning and sharing exchanges with fabricator/installers.
One key initiative we have undertaken is the establishment of a world-class learning facility located just a few miles from our manufacturing plant. The Academy at Cambria learning facility is equipped with the latest technology and equipment to enable fabricators to exchange with us and others, further advancing the process of making our world-class surfaces from start to finish. This allows all of us to gain hands-on experience in cutting and shaping quartz, installing quartz surfaces collaboratively with our fabricator partners. Importantly, we interchange and learn about the unique characteristics of our products in a mutually beneficial partnership in study of the fabrication and installation field.

"Key consideration when developing new product lines is always ensuring that our products are not only visually appealing, but also highly functional and durable," said Marty Davis, Cambria Chief Executive Officer (CEO). | Photo courtesy of Cambria
At the Academy at Cambria, we also provide ongoing educational/learning exchange resources to fabricators through a variety of channels. This includes online tutorials, webinars and instructional videos that cover various topics related to working with quartz surface products, including safety, cutting, shaping and installation.
Moreover, we work closely with our network of fabricators to ensure that they have access to the latest information, optimal approach related to safely and proficiently cutting, edging, polishing, finishing and installing quartz surfaces. This includes providing technical support and answering any questions they may have about our products and processes.
Overall, our commitment to exchanging knowledge with fabricators and learning from our fabricators about finishing quartz surface products is a key factor in our ability to deliver high-quality, durable and visually stunning products to our customers. By providing comprehensive learning centers and ongoing support, we ensure that our products are crafted to the highest standards of quality and precision.
LS: We are the first in the industry to offer fabricators cutting-edge programs that provide training and guidance on fabricating our quartz, porcelain and health and safety. Our Master of Stone program is a free online certification that teaches fabricators about health and safety and best practices for cutting quartz and porcelain. Also, with the recent launch of our porcelain line, our best-in-class global leadership team held training sessions across the U.S. and Canada to provide hands-on training in person.
SW: How different is the process of cutting quartz compared to porcelain slabs?
LS: Many know when fabricating quartz, the strength of the material holds up throughout the fabrication process. While some may consider porcelain a fragile material, we have reinforced our slabs with a fiberglass-mesh backing to increase durability throughout the fabrication process. When combined with our Master of Stone training program, we offer a product and educational experience that makes cutting porcelain easier than ever before.
SW: For fabricators hesitant to start cutting porcelain, what words of encouragement do you have for them?
LS: Caesarstone is here to equip our fabricators with guidance and training through our Master of Stone program to support them throughout their journey working with porcelain. We just hosted an East and West Coast fabrication tour where our global leadership team worked hands-on with fabricators to learn best practices to cut porcelain. Much of the feedback we received from fabricators nationwide was that our porcelain is flexible and holds up during the fabrication process because of the fiberglass mesh backing. Our expert team is always available to guide, teach and visit the shops to provide hands-on assistance. At Caesarstone, our priority is building trust in the fabricator community and developing long-lasting relationships by supporting them with thorough training and a superior product.

"Many of our designs are based on what one may see or find in nature, which is our biggest inspiration," said Shapiro. "We believe that materials from the Earth should bring tranquility and warmth into any space, and we want to give our customers that experience in their home." | Photo courtesy of Caesarstone
SW: Do you find quartz is being used more now for outdoor applications than in the past?
AT: Quartz has always been a popular choice for a wide range of indoor applications, but in recent years, we have noticed a growing trend towards its use in outdoor applications as well. This is due in large part to the inherent qualities of quartz, which make it one of the best surfaces in the world to use for so many projects.